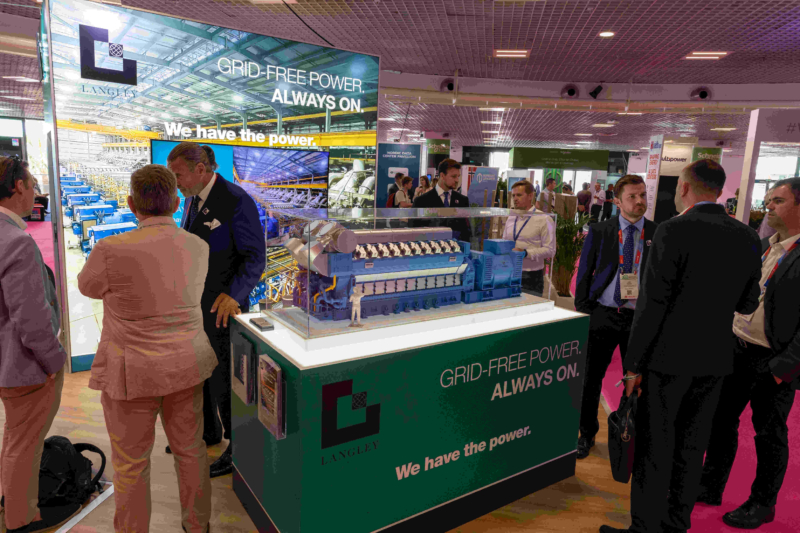
SOLUTIONS FOR A SUSTAINABLE FUTURE
At Bergen Engines, we recognize the urgent need for sustainable solutions. We understand the critical role that energy plays in our daily lives and its impact on the environment. We are committed to championing clean and responsible energy solutions that power a more sustainable future.

As the world shifts towards flexible and sustainable energy solutions, Bergen Engines is driving change by innovating with hydrogen, ammonia, and other eco-friendly fuels.
We conduct innovative studies on low-carbon future fuel options and explore new applications, including hybrid-renewable systems, to meet the demands of tomorrow. Our dedication is to a future that prioritizes environmental sustainability.
We continuously strive to enhance energy efficiency across our operations while reducing our consumption. Additionally, we actively work to reduce greenhouse gas emissions from our engines through innovative technologies and practices, minimizing our contribution to climate change, both for ourselves and our valued customers.
Within the maritime and energy sectors, there is an urgent need to decarbonize through new methods and trusted, efficient solutions. Since 1943, Bergen Engines has consistently evolved to stay ahead of the ever-changing market landscape. Our ability to anticipate, develop, and construct engines with low-emission technologies at the forefront of our design remains unmatched. With a global footprint and a portfolio of references on all continents, our reputation for reliability and unwavering commitment to producing engines for the future have solidified our position as a leading producer of medium-speed engines.
Did you know...
FUTURE FUELS
Future fuel options are important for the green transition because of their potential to address the challenges associated with traditional fossil fuels and contribute to a more sustainable and environmentally-friendly energy landscape. This is why Bergen Engines is working to ensure our technology performs with the same reliable efficiency, no matter the fuel source chosen by our customers. Visit our Future Fuels page to learn more about ongoing research in Hydrogen, Methanol, and Ammonia.


LOW-CARBON APPLICATIONS
On Land, Bergen Engines is finding new focus in supporting hybrid energy systems that combine multiple sources of renewable energy, such as solar panels, wind turbines, and energy storage. These systems are designed to maximize the use of clean and sustainable energy sources, with Bergen Engines ensuring reliable power generation and supply. By integrating various renewable resources with our low-emission and high efficiency units, we can enhance energy resilience and reduce reliance on conventional fossil fuels.


LATEST NEWS

| Recent News
Parent Company Interim Report Released Today

| Our stories, Recent News
Bergen Engines Adds 120 Jobs as Demand for Low-Emission Power Surges

| Events, On Land., Recent News
Bergen Engines Represents Norway at Ukraine Recovery Conference

| Events, At Sea., Recent News
Bergen Engines Showcases Innovation and Leadership at Nor-Shipping 2025
ISO CERTIFICATES
Bergen Engines holds the following ISO Certificates under Bureau Veritas:
- ISO 9001: Quality
- ISO 14001: Environment
- ISO 45001: Health & Safety
View the certificates here.
Contact us
Please fill in your contact details below and we’ll reply as soon as we’re able.

Contact us
Please fill out the enquiry form, and our dedicated team will promptly attend to your request